Case Study: Enhancing Productivity with Laser Welding in the Sheet Metal Industry
- mohamedjashim
- Nov 6, 2024
- 4 min read
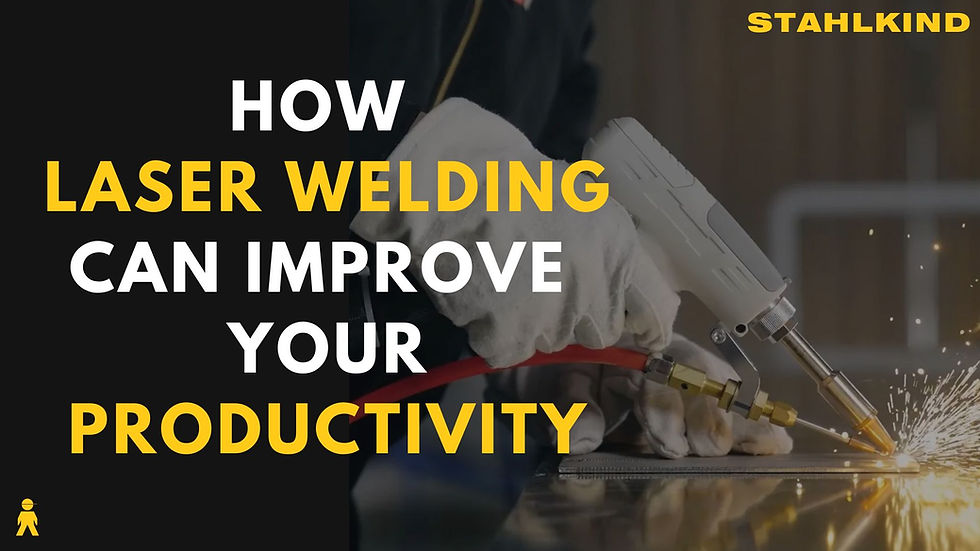
Introduction: The Need for Innovation in Sheet Metal Fabrication
In the sheet metal industry, especially in the manufacturing of lower-thickness metal enclosures and high precision components, precision, speed, and efficiency are key. Traditional welding techniques like MIG (Metal Inert Gas) and TIG (Tungsten Inert Gas) welding have served the industry well, but they come with significant challenges—especially when dealing with thinner materials. This case study explores how the adoption of laser welding technology can revolutionize the fabrication process for thin-gauge sheet metal, improving both productivity and quality while reducing labor requirements.
Key Benefits of Laser Welding for Thin Sheet Metal and Robotic Components
1. Precision and Control for Thin Materials
Minimal Heat Distortion: One of the major advantages of laser welding in sheet metal fabrication is its ability to focus heat on a small, precise area. When welding thinner materials like 1mm to 3mm sheets commonly used in enclosures and robotic components, traditional methods can cause significant heat distortion, warping the material. Laser welding’s precision minimizes these issues, preserving the integrity of the metal.
No Burn-Through: Lower-thickness materials are prone to burn-through with MIG or TIG welding due to excessive heat input. Laser welding's control over heat ensures that thin sheet metal is welded cleanly without damaging the structure.
2. Increased Productivity and Throughput
Higher Welding Speeds: Laser welding can achieve speeds up to 10 times faster than conventional welding methods when working with thin sheet metal. This drastically reduces production time, making it possible to fabricate more enclosures and robotic components in a shorter period.
Automated Processes: Laser welding systems can be fully automated and integrated into production lines, leading to higher throughput. Automation reduces human intervention, which not only speeds up the process but also ensures a consistent quality of output.
3. Superior Quality of Welds
Clean and Precise Welds: When manufacturing products such as thin sheet metal enclosures for electronics or precision robotic components, high-quality welds are essential. Laser welding produces smooth, accurate joints with minimal spatter or deformation. These clean welds are especially important in applications where aesthetics or precision are critical.
Minimal Post-Weld Finishing: Traditional MIG or TIG welding may require extensive post-weld finishing, such as grinding and polishing, to remove imperfections. Laser welding’s precision results in welds that need little to no post-processing, saving valuable time and labor.
4. Adaptability to Complex Designs
Intricate Welds for Robotic Components: Modern robotic components often have intricate designs and require welding in hard-to-reach or complex areas. Laser welding’s precision and ability to weld at different angles and in tight spaces make it the ideal choice for these complex assemblies. This allows manufacturers to build robotic components with complex geometries without compromising on the strength or appearance of the welds.
Fine Details for Enclosures: In industries where enclosures must be sleek and well-finished, such as in electronics or medical devices, laser welding provides the high precision required for delicate designs and fine details.
5. Reduced Labor Costs and Flexibility in Workforce
Low-Skilled Labor Capabilities: One of the most significant advantages of laser welding is its ability to be operated by lower-skilled labor due to its automated nature. In a sheet metal fabrication environment, this reduces the reliance on highly trained welders. With simple training, operators can manage automated laser welding machines, further cutting down on labor costs.
Reduction in Human Error: Since much of the process is automated, there is less opportunity for mistakes. Traditional welding relies heavily on the skill of the welder, but laser welding’s automation ensures consistency in each weld, reducing the variability caused by human error.
A welder in our factory effortlessly meeting his daily targets
Smaller weld bead size means less time in post weld finishing
Real-World Impact: Meeting Customer Demands with Speed and Quality
For customers in industries requiring thin sheet metal enclosures or precision robotic components, laser welding delivers clear advantages:
Faster Lead Times: With increased welding speeds and automation, production cycles are significantly shorter. Customers benefit from reduced lead times and faster delivery of their products.
Improved Product Quality: The precision of laser welding means that customers receive products with cleaner welds, fewer defects, and greater consistency—resulting in less rework and higher overall satisfaction.
Cost-Effective Solutions: By reducing the need for skilled labor and post-weld processing, laser welding brings down production costs. These savings can be passed on to customers, offering them more competitive pricing without sacrificing quality.
Conclusion: The Future of Sheet Metal Fabrication
For manufacturers working with thin sheet metal and producing precision robotic components, laser welding offers a transformative solution. The technology delivers faster production, higher quality welds, and the ability to work with lower-skilled labor, making it a game changer in an increasingly competitive industry. As customer demands for speed and quality continue to grow, adopting laser welding is not just an advantage—it’s essential to staying ahead.
Interested in learning how laser welding can enhance your production process?
Connect with us to discover how we can help you meet your quality and productivity goals with the latest in welding technology.
Comments